Sleipner Finland and Komatsu Poland have entered into a representation agreement for innovative transport solutions for moving mining and construction machinery in the Polish market. Sleipner’s patented DB Series lowbed trailers and E Series dollies make operations in mines and quarries significantly more efficient compared to traditional transfer solutions, such as driving on tracks or using traditional road trailers. The new agreement covers both product lines.
Sleipner Finland’s transport solutions extend the operational usage time of heavy mining and construction machinery and reduce the life cycle costs of moving equipment, for example thanks to the easier maintenance they enable.
“With this agreement, we want to show our customers that they can rely on us in every aspect of their quarry and mining operations, regardless of the machines they use,” says Andrzej Tokarczyk, Deputy Sales Director at Komatsu Poland.
Komatsu Poland offers a comprehensive range of machinery tailored for the mining sector, establishing itself as a market leader in mining equipment supply. In addition to their extensive equipment offerings, Komatsu Poland provides comprehensive servicing solutions, ensuring optimal performance and reliability for all our machines.
Tokarczyk has worked for Komatsu Poland for eighteen years, and his main focus is major customers and the big machine business. Komatsu Poland has a very large market share in the 50-tonne class.
“The economic situation in the mining industry in Poland is quite healthy. Demand is currently down perhaps 20 percent compared to 2 or 3 years ago, but we have some pending deals for 2024 and 2025 and hopefully we can recover our income and profit,” Tokarczyk estimates.
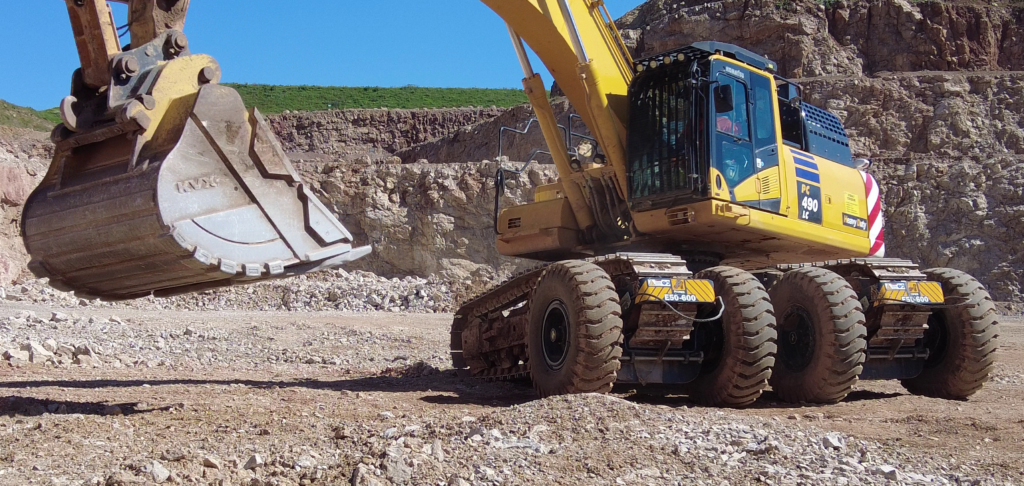
First Sleipner Finland E Series dollies sold to the Holcim mine
The first Sleipner E50 dollies are currently being used with a Komatsu PC490 excavator at the HOLCIM mine in Poland since last autumn. The Sleipner E50 dollies has eliminated unnecessary driving on tracks, made operations more efficient and reduced wear and tear on undercarriages.
“I was on site at the end of February and the feedback was positive. The customer is getting used to using the Sleipner E50 and is all around happy with the purchase,” says Conrad Caldwell, Sales Director EMEA at Sleipner Finland.
The Sleipner DB Series in turn offers a range of agile lowbed trailers that can be used in even the most challenging conditions at mines, quarries and excavation sites. The newest edition to the DB Series is the compact DB45 offroad trailer, which has been designed for moving surface drills and bulldozers weighing up to 45 tonnes.
The DB45 trailer is not permanently connected to the towing unit. It is towed by an articulated dump truck (ADT). The trailer can be connected to the ADT whenever needed, leaving the ADT available for normal tasks at other times.
Connecting and disconnecting the trailer only takes a few minutes. The concept is unique and makes it possible to access places where heavy machinery could not previously be transported. Articulated dump trucks are agile and have six-wheel-drive, allowing them to be operated even in difficult terrain.
The Sleipner DB Series enables fast and safe loading and transporting, while also providing flexibility for daily production planning. Drills and dozers can be picked up and delivered efficiently to the exact place where they are needed.
More efficient production in even the most challenging conditions
Tested in both freezing northern climates and the extreme southern heat, Sleipner products are famous for their reliability in all conditions. Their structural and component solutions highlight a long service life, low life cycle costs, global availability and easy maintenance.
“What used to be a time-consuming process to get from one site of the operation to the other is safely sped up. Customers see a significant reduction in the overall running costs of their equipment and a significant decrease in CO₂ emissions,” Caldwell explains.
“From a customer perspective, the increase in productivity, reduction in undercarriage maintenance costs and quicker relocations are the main benefits. Equipment can now be moved efficiently from the bottom of the pit to the workshop and onwards to the next position,” Caldwell continues.
For more information
Contact person Komatsu Poland
Andrzej Tokarczyk, Deputy Sales Director
andrzej.tokarczyk@komatsupoland.pl
Contact person Sleipner Finland Oy
Conrad Caldwell, Sales Director EMEA
conrad.caldwell@sleipner.com